Choosing the right steel alloy for your application is critical to ensuring durability, cost-effectiveness, and performance. With a vast array of steel alloys available, the selection process can seem overwhelming. This article will guide you through key factors to consider and highlight common steel alloy types to help you make an informed decision.
Understanding Steel Alloys
Steel is an alloy of iron and carbon, with additional elements such as chromium, nickel, manganese, or molybdenum added to impart specific properties. These variations create different categories of steel alloys suited for a wide range of applications.
Key Factors to Consider
When selecting a steel alloy, you need to assess your application’s requirements. Key considerations include:
- Mechanical Properties
- Strength: How much stress can the material handle before deforming?
- Hardness: Resistance to scratching, wear, or indentation.
- Ductility: Can the alloy stretch without breaking?
- Toughness: Ability to absorb energy and resist impact.
- Environmental Factors
- Corrosion Resistance: Does your application involve exposure to moisture, chemicals, or extreme temperatures?
- Temperature Stability: Will the alloy maintain its properties under high or low temperatures?
- Fabrication Needs
- Does the alloy need to be weldable, machinable, or heat-treatable?
- Cost: Balancing performance with affordability is essential.
Common Steel Alloys and Their Applications
- Carbon Steel
- Low Carbon (Mild Steel): Affordable and easy to machine. Common in construction, automotive panels, and general-purpose parts.
- High Carbon: Hard and wear-resistant, used in cutting tools and springs.
- Alloy Steel
- Contains additional elements like chromium, nickel, or molybdenum to improve strength and resistance.
- Applications: Aerospace parts, automotive components, and power plants.
- Stainless Steel
- Known for excellent corrosion resistance due to high chromium content.
- Applications: Kitchenware, medical devices, and marine equipment.
- Tool Steel
- High hardness and wear resistance, often used in cutting, stamping, and forming tools.
- Applications: Molds, dies, and industrial tools.
- Maraging Steel
- Ultra-strong and tough, often used in aerospace and defense industries.
- Applications: Missile casings, high-performance gears.
Case Study: Choosing a Steel Alloy
Imagine you’re designing a marine propeller. The alloy must resist corrosion from seawater, maintain strength under high pressure, and be cost-effective. Stainless steel, specifically grades like 316 or duplex stainless steel, would likely be the best choice.
Tips for Selecting the Right Steel Alloy
- Consult Standards: Review industry standards such as ASTM or ISO for material specifications.
- Test Samples: Obtain small quantities of alloys to test under your specific conditions.
- Seek Expert Advice: Metallurgists and material suppliers can provide tailored recommendations.
Conclusion
Choosing the right steel alloy depends on understanding your application’s specific demands and the unique properties of various alloys. By assessing mechanical properties, environmental conditions, and fabrication needs, you can select a material that ensures performance, longevity, and cost-efficiency.
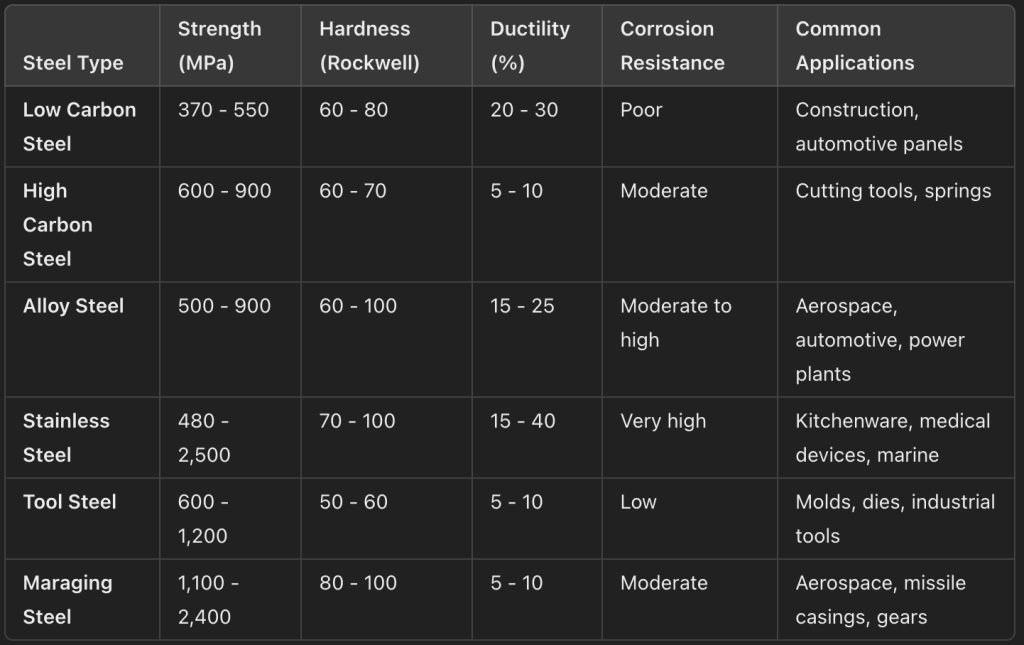
Cover photo credit: https://www.wieland-diversified.com/